TQC provides air decay leak testing solutions for all types of components to measure air pressure decay.
For these solutions, standard leak testing measurement instruments are incorporated to find a change in air pressure or air flow on the components being tested.
TQC offer test pressures between vacuum and, typically, 16bar (150psig) as standard, with leak testing measurements down to a resolution of 1 atm.mm3/sec. All air decay leak test parameters may be programmed into the instruments that are supplied as part of the solution, and the resulting data is available for subsequent Statistical Process Control (SPC) analysis.
When comparing leak testing methods, air decay testing offers the following:
Air decay leak testing – Overpressure (above 0 bar)
- The lowest cost solution
- Simple to understand results data
- Direct value results
- Direct calibration
- Temperature-dependent process (alternative test method is vacuum testing)
- Best when used when component under test is stable
Overpressure leak testing is suitable for the following component and environment applications:
- Volumes up to 3 litres
- Stable temperature parts
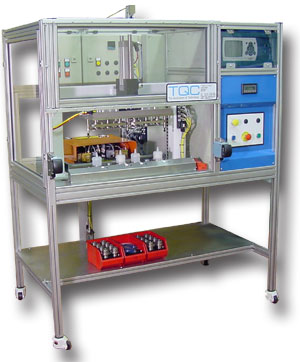
Read more about our High Pressure (Over 6 bar) and Low pressure (0-6 bar) leak testing machines.
Air decay leak testing – Vacuum (below 0 bar)
- Offers more robust leak testing
- Greater integrity of data
- Limits temperature dependency effects
- Assists sealing loading
- Reduced stabilisation time
- Often a faster throughput
- Indirect leak calculation
- Offers complex fault detection
Vacuum leak testing is suitable for the following component and environment applications:
- Volumes up to 5 litres
- Parts subject to moderate temperature variation

Read more about our Vacuum Leak Testing machines.
Flow Testing
For larger leaks and larger internal test volumes one can use a flow testing instrument. These instruments maintain an accurate test pressure whilst recording the gas flow with a flowmeter. Depending upon the test volume this tends to be a technique for checking larger leaks.