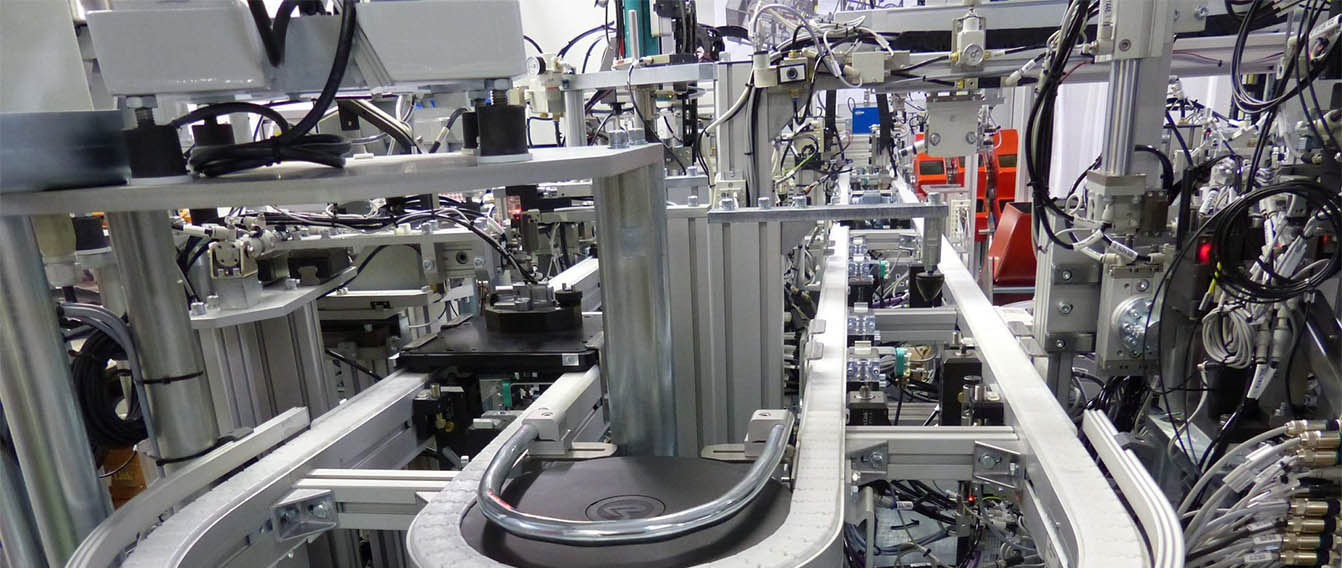
Automated Assembly & Test System for Timing Chain Tensioner
Machine supplied: Fully Automated Assembly and Test Solution
Client: Leading Power Transmission Component Manufacturer.
Part: Chain Tensioner
Overview: This automated assembly and test system was designed and manufactured to give the customer the ability to produce chain tensioners at a rate of 225 per hour. TQC developed this automated production line alongside the client to allow them to supply quality, tested parts to their customers.
This palletised system sequentially assembles and tests the tensioner with final parts fed out onto a pallet conveyor ready for manual packing.
The main body casting is fed into the system via a pallet track system that is manually loaded; a gasket is fed from a magazine, with all other components being fed from bulk using 11 bowl feeders.
Automated assembly operations that are carried out during the machine sequence include, check valve testing, spring loading, pivot pin insertion (hydro-pneumatic pressing), part pick and placement, axi-rad insertion, bolt screwing to depth, percussion marking and various vision and sensor checks.
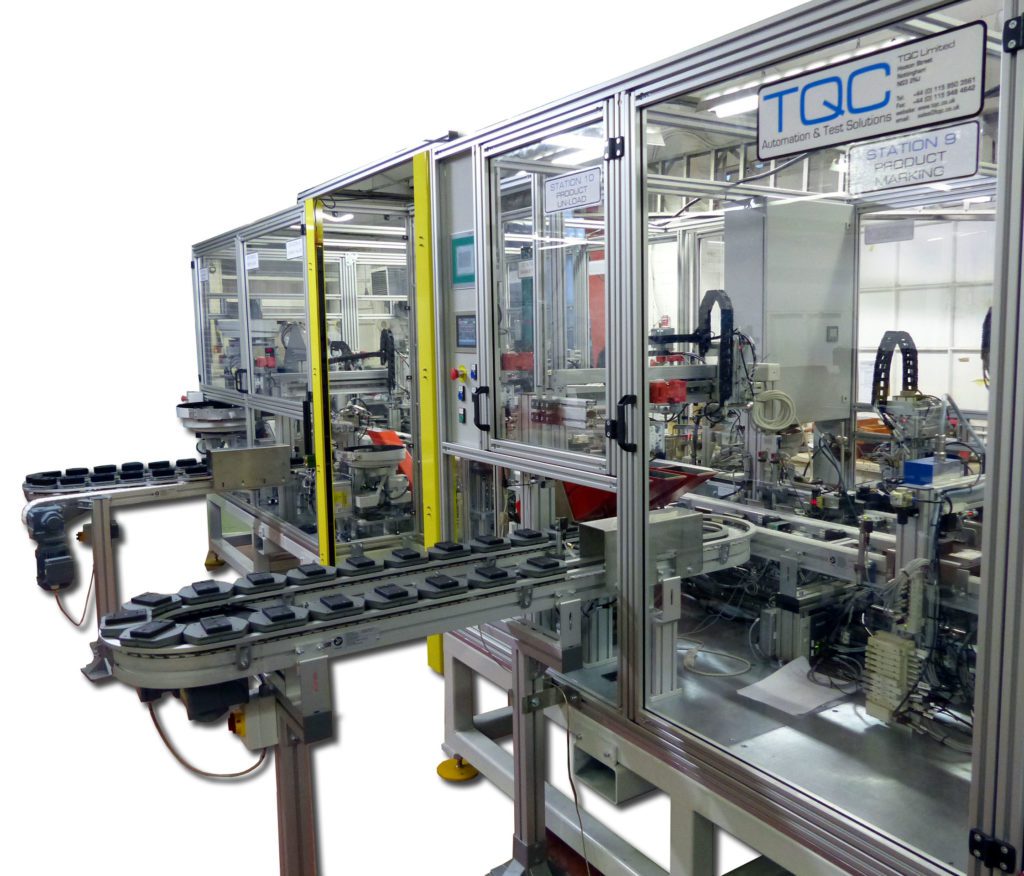
Automated Assembly and Test Stations located around the Pallet Conveyor carry out the following –
- Station 1 Gasket Pick and Place with Manual Intervention Area
- Station 2 Body In-feed and Check-valve Test
- Station 3 Plunger and Plunger Spring Measure / Assembly & Insertion
- Station 4 Cam Spring, Cam and Cam Pin Insertion
- Station 5 Cam Pin and Link Plate Press
- Station 6 Assembly Validation and Stopper Pin Insertion
- Station 7 Axi-Rad Insertion
- Station 8 Bolt Insertion
- Station 9 Pass Marking
- Station 10 Out-feed with Bolt Length Inspection
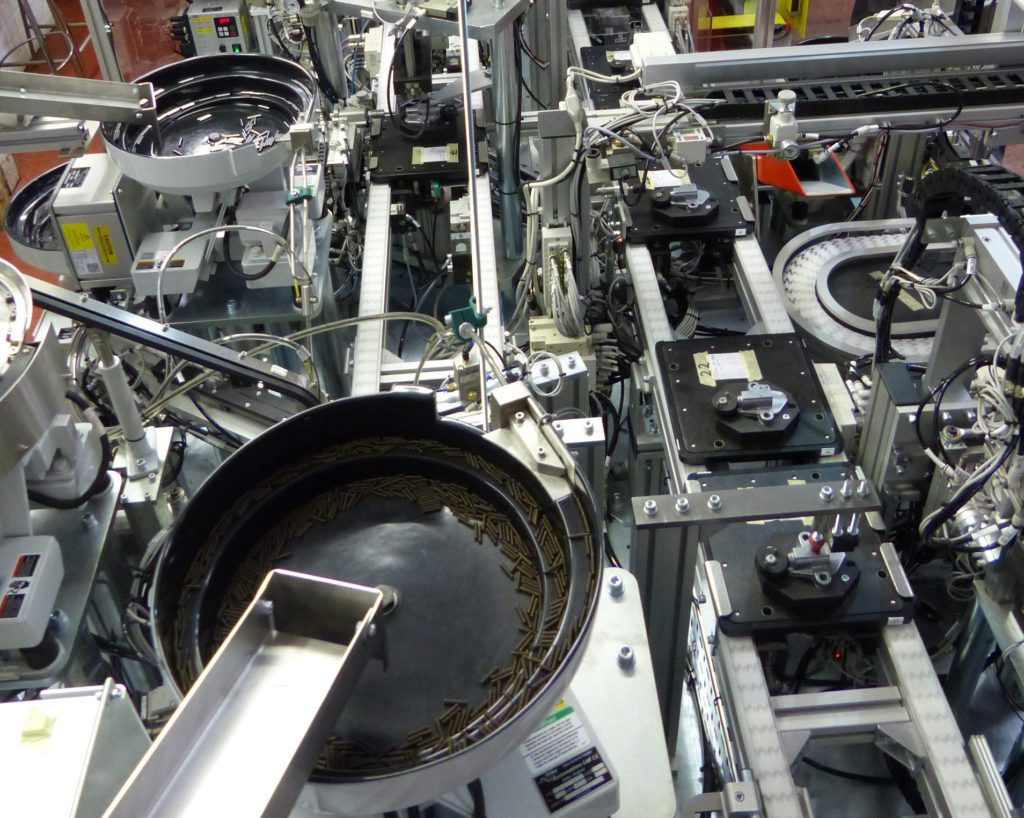
Pallet Conveyor Systems
The main body casting is handled using a pallet infeed loop, the main assembly system uses a larger pallet-based loop conveyor and the finished assembly is handled by a third pallet loop conveyor. To minimise the machine footprint the body casting tooling was designed to accommodate 2 bodies in a single pallet. On the main system pallet tooling an onboard part clamp was incorporated to lock the body in place.
Bulk Feeding of Components
The main components are fed from bulk using bowl feeders, linear tracks and escapements. Each bowl can be topped up during machine operation to allow fully automatic running, low level sensors indicate when the bowl need to be topped up.
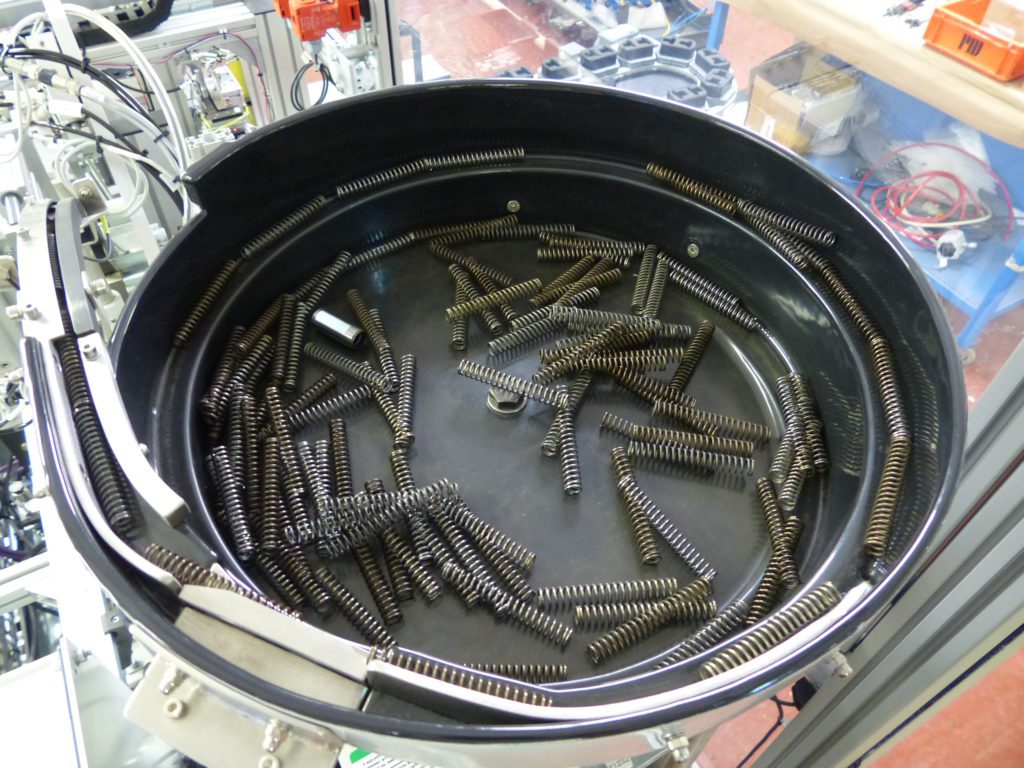
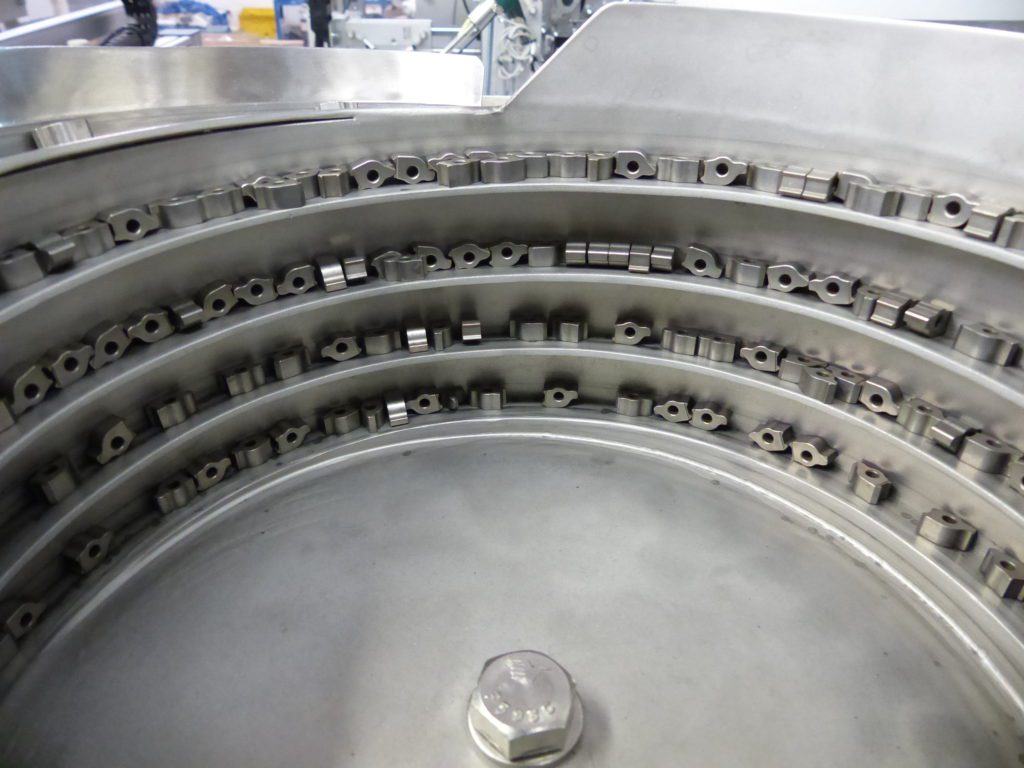
Automated Assembly Operations
The system has numerous complex mechanisms for the automated assembly of the timing tensioner. Individual parts and picked and placed using pneumatic and servo driven actuators as necessary. Plastic inserts and bolts are handled in pairs with the bolts screwed to a known position to locate through the gasket. Some stations have pre-assembly of parts prior to fitting into the main body, these are offline mechanisms that operate concurrently. The cam pin and link plate use a hydro-pneumatic press to secure them in place complete with load and position monitoring.
Process Verification & Part Marking
The system checks the assembly process at various points on the system with the control system tagging each tensioner as a pass or fail. Sensors and vision systems are used to check that components are within tolerance and that assembly operations are performed correctly. A function test is carried out to ensure the tensioner operates as required. The final process prior to unloading is part marking of the tensioner using a percussion marker. All failures are unloaded into one of 6 reject chutes dependant on the type of fault.
Automated Assembly Control System
The assembly and test system is controlled via an Omron PLC and HMI.
To view a printer friendly format please click below
Chain Tensioner Automated Assembly System
If you have an application that could benefit from TQC’s expertise in automated assembly and automation please contact us by email or phone via the contact details