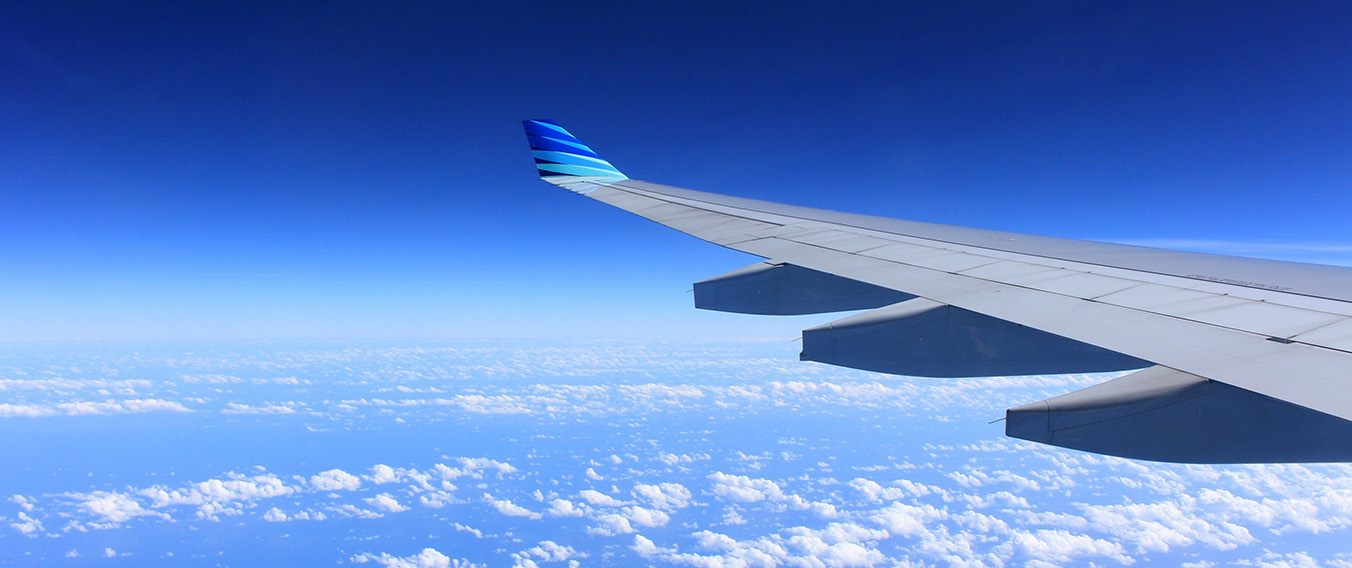
Aircraft Wing Fuel Tank & Pipework Test Equipment
Client: Leading Aircraft Wing Manufacturer
Part: Aircraft wing fuel tanks and pipework.
Machine supplied: 3 bespoke freestanding portable semi automatic test systems
Overview: These systems were designed and manufactured in order to give the customer the ability to test aircraft wing fuel tanks and pipework assemblies within their production environment. TQC developed this system alongside the client to allow them to supply quality, tested parts to their customers.
The equipment includes 3 bespoke freestanding portable semi automatic systems :-
- Hydrogen Tracer Gas Leak Test Bench for leak testing large volume carbon fibre aircraft wing fuel tanks.
- Fuel Pipe Leak Test Bench to perform nitrogen leak tests on wing fuel, fire extinguisher and other pipework.
- Hydraulic Pipework Test Bench for flushing and pressure testing wing hydraulic pipes.
For a printer friendly copy of this page, please click below
Aircraft Wing Fuel Tank & Pipework Test Equipment
Aircraft Wing Hydrogen Tracer Gas Leak Test Bench
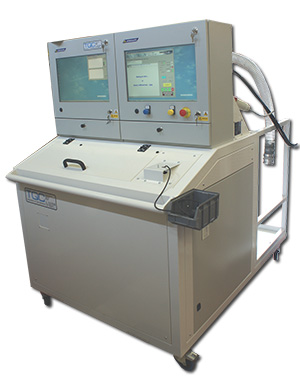
This system is designed to test the integral fuel tanks within the wing structure. The test system checks for leaks
- from the internal tanks to the outside through the
- various seams and rivets in the aircraft wing
- between the two main tanks
- from each tank into a dry bay within the wing
The test equipment includes a series of fittings and sealing bungs specifically designed to blank off the wing structure orifices and support the leakage testing
The test system consists of 2 hydrogen sniffing instruments with a gas dosing and circulation system. This is all controlled by a sophisticated double PC system with Production Visual Aid images and text to guide the test engineer through the complex set of operations to be performed on the aircraft wing under test.
The wings are subjected to an automatic ‘gross leak’ pressure decay test before the hydrogen tracer gas-sensitive leak check is performed.
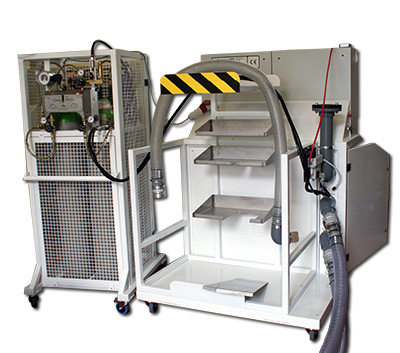
The system also has a bar code scanner to identify both the wing and the test operator. The system interfaces to the clients Management Information System for archiving test results, downloading test protocols written offline and for authorisation of test personnel.
The gas handling system uses a four gas bottle supply system of 5% Hydrogen in 95% Nitrogen with automatic changeover. The wing tanks, being many thousands of litres need a significant supply of test gas even though the wing test pressure is only 2 psig. The gas handling system has gas pressure monitoring to indicate when a gas bottle changeover has occurred.
The gas handling system also includes a circulation system to ensure an even mixture of the test gas throughout the tank under test. While the wing is pressurised, the pressure is monitored to ensure that there is no gross leak to prevent a significant loss of test gas.
Safety is of paramount importance, and so the gas handling systems are fitted with pressure monitoring and pressure relief systems to prevent over pressurisation. In addition, the level of hydrogen and oxygen is monitored to not only ensure a homogenous gas mixture but also to ensure that the tank environment is safe for operators at the end of the purge cycle and does not present any danger of asphyxiation.
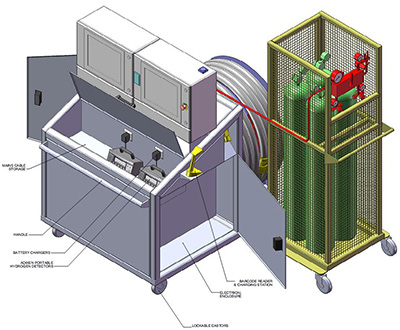
When testing a specific tank, the operators are instructed by the control system displaying production visual aids and text instruction through the processes of :-
- ‘dressing’ the wing—connections, sealing bungs, jumpers
- gross leak test by pressure decay monitoring
- tracer gas pressurisation and mixing
- tracer gas leak test using sniffer probes
- purging
- ‘undressing’ the wing
During the leak testing, the test sequence will not proceed until the operator has confirmed the sniffer probe pass / fail status.
Aircraft Wing Fuel Pipe Leak Test Bench
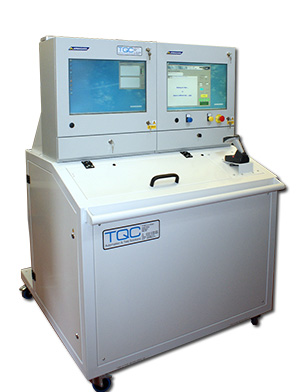
This machine is a blockage and pressure test system to check pipework through the wing for fluid and pneumatic systems.
- Test pressures range between 20 psig and 1,000 psig of both Nitrogen and compressed air.
- The equipment supplied includes a set of quickfit adapters, blanks and connection pipes to enable rapid connection to the various pipe runs.
- Sophisticated PC control system guides the test engineers through each of the individual tests.
The following tests make up a complete test for the array of pipework in the wing :-
- ‘dressing’ the pipework
- blockage detection of the branches of each pipe run
- Pressure decay leak test
- ‘undressing’ the pipework
Each of the 8 different pipe runs can have a specific test pressure within the 20 to 1000 psig range of the machine.
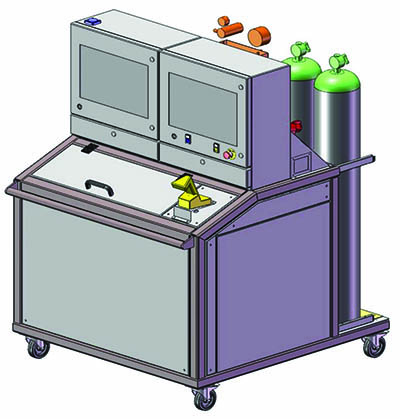
Aircraft Wing Hydraulic Pipework Test Bench
The hydraulic pipework test system is for flushing and pressure testing the hydraulic piping systems and equipment that pass through the wing. The hydraulic test system is based on a sophisticated Moog pump system that uses electronic control to output low pressure / high flow for flushing and high pressure / low flow for pressure testing. Control is again by a sophisticated PC system.
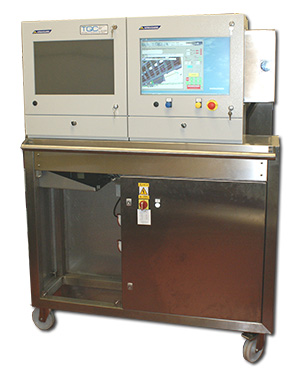
The hydraulic test system had 4 functions :-
- Nitrogen gas gross leak test
- Turbulent flow flushing
- Hydrostatic pressure testing
- Nitrogen gas purge at the end of testing
The hydraulic pipework test includes the following:-
- ‘dressing’ of the pipework, this can include
- jumpers to bypass internal components
- nitrogen gross leak test
- filling with Skydrol and then flushing at Reynolds number of 4000 (turbulent flow) until the contamination particle counter monitor confirms the system cleanliness
- high pressure leak test (pressure decay, upto 4500psi)
- nitrogen purge to recover the Skydrol
- ‘undressing’ the pipework
The result of each test was monitored and recorded onto the PC system for full traceability together with bar code scanning of the wing under test and of the test engineer that is performing the testing. The equipment supplied included a set of adapters, blanks, jumpers and connection pipes, all to aerospace specification, to test the various pipe runs.
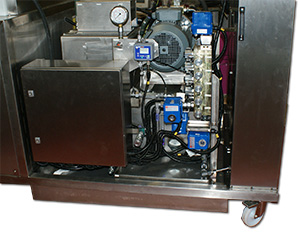
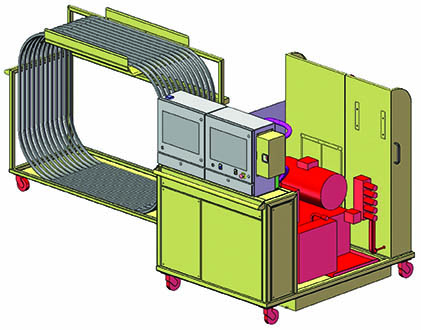
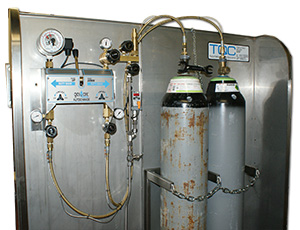
Additional Feature of All Three Test Systems
An important requirement of the three test system is that the test sequence definition is flexible and able to be changed by a suitably authorised end user engineer. In addition, tests can be added or deleted as the need arises.
More Information
For more information about this area of testing please visit the TAMI project webpage here. TAMI, Test for leakage identification on aircraft fluid mechanical installations, was a project TQC was heavily involved with leading partners Airbus Defence and Space (ADS).