TQC have designed and produced a number of sophisticated rotary assembly machines and systems for several demanding applications.
Rotary assembly machines, also known as rotary tables or indexing systems, incorporate location tooling for the parts that is captive to a dial plate and individual stations that incorporate technology modules such as part feeding, robots, vision measurement to automatically carry out sequential operations. The advantages of using an indexing or continuous motion dial plate with a series of fixtures are the relatively low cost and rapid indexing of the transport system. Fully automatic systems can reach throughputs of 400 a minute or more when continuous motion is used.
The part or parts of the assembly are indexed around a system until the required operations have been completed. Finished parts are unloaded onto a conveyor system for either manual handling or automated packing.
The use of a rotary assembly and test machine is advantageous when the cycle time is greater than 5 seconds and an operator is best used for some of the assembly processes.
For a fully automatic system, part feeding and handling can be integrated or for semi-automatic operation an operator can be used to position difficult to feed parts into the fixtures or used as a final inspection operation, or both. Rotary or carousel type assembly machines also offer a compact form of semi automatic machine.
The nest tooling tends to be “dumb” because of the continuous rotation. The assembly and test tooling is usually arranged in a radial fashion secured outside of the dial plate. Twin or even multiple track nests are possible, as are interchangeable nests for different variants.
TQC have considerable experience in engineering rotary assembly machines, combining sophisticated test and assembly on the same machine.
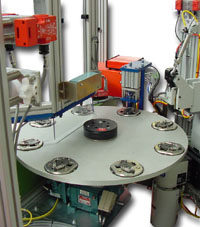
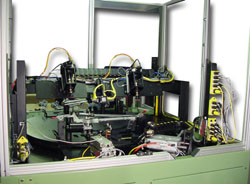
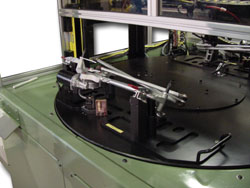
The business cases that are addressed by installing a rotary system into your production facility are that operations can be carried out fully automatically with the system producing complete products so there is no work in progress (WIP) produced during normal running. There is the flexibility of changing the tooling to accommodate new variants.
A rotary assembly system can replace some or all manual labour allowing production running costs to be reduced. Additional benefits include that the operations can be quality assured and checked automatically. This being pertinent to many production environments including the pharmaceutical and medical sectors, the automotive sectors and aerospace and defence industries.
A good example of a rotary table assembly system can be seen in our case studies.